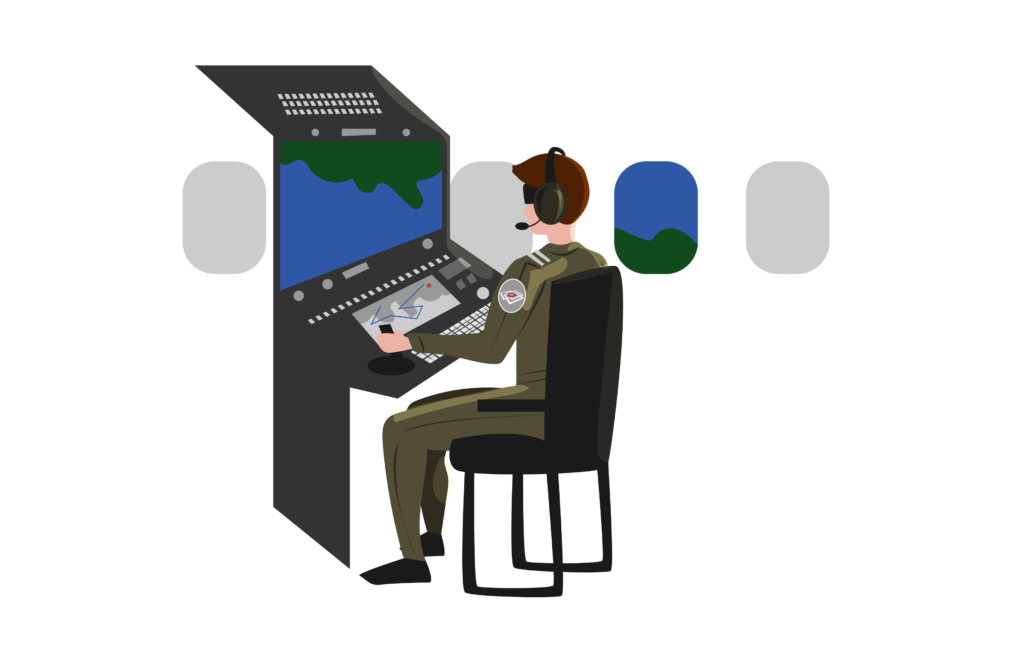
Whether you’re missionizing a new platform or retrofitting an existing one, choosing a new mission computer is a consequential decision—one that’s often more complicated than it first appears.
Not only must you weigh the cost and the capabilities of the units themselves. You also need to consider customization, installation, and total cost of ownership over the life of the platform.
That’s why we’ve put together this guide for you. If you’re looking for a new mission computer to run AIMS-ISR on your platform, we want to help you make the right decision. While we don’t supply avionics hardware, we’ve worked with countless systems integrators who do, and we’ve seen almost every conceivable combination.
In this guide, we’ll examine seven not-so-obvious features we recommend you should consider during your evaluations. These seven key features will not only provide immediate value but also deliver significant savings over the system’s lifecycle.
We hope you will find this guide useful when choosing your next mission computer.
Sincerely,
The Team at CarteNav Solutions
Download the Guide + Checklist
The printable guide + checklist is now available!
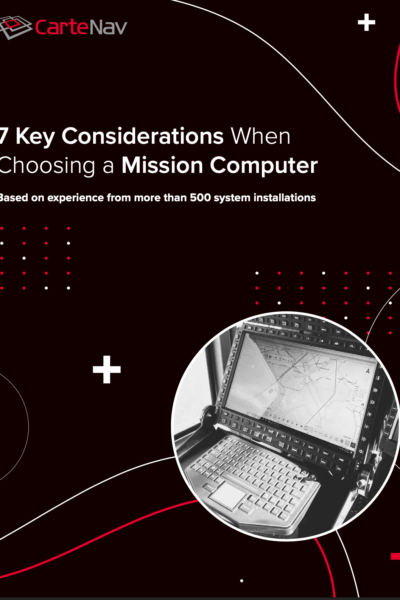
Key consideration #1: Customizability
Look for end-user customizability.
You’ll want to see numerous configuration options. You don’t want to be tied to just one format when it comes to features like video formats and serial ports.
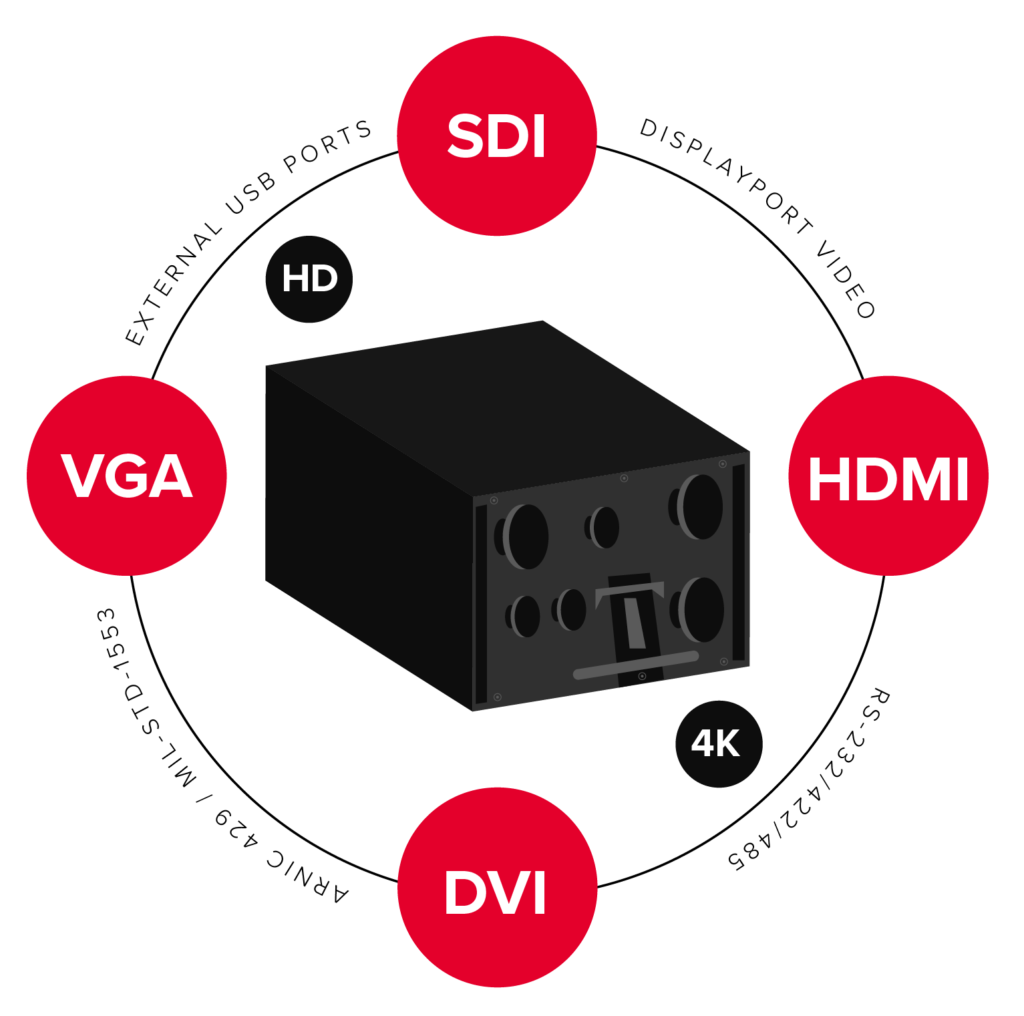
Is there support for VGA, DVI, SDI, HDMI and DisplayPort video? HD and 4K resolution? What about RS-232/422/485 serial ports? External USB ports? Are there options for ARINC 429 or MIL-STD-1553 bus support?
End-user customizability provides flexibility when retrofitting a new computer into an existing system or choosing additional components for a new system. It also reduces costs by making easy modifications to the unit at the factory rather than forcing the integrator to adapt the rest of the system to the mission computer’s limitations.
These options should be designed into the system as build options when ordering; a factory technician need only make small adjustments during final assembly to fulfill your requirements. Build options mean you won’t incur expensive NRE charges or delivery delays for those changes.
Key consideration #2: Fully tested build options
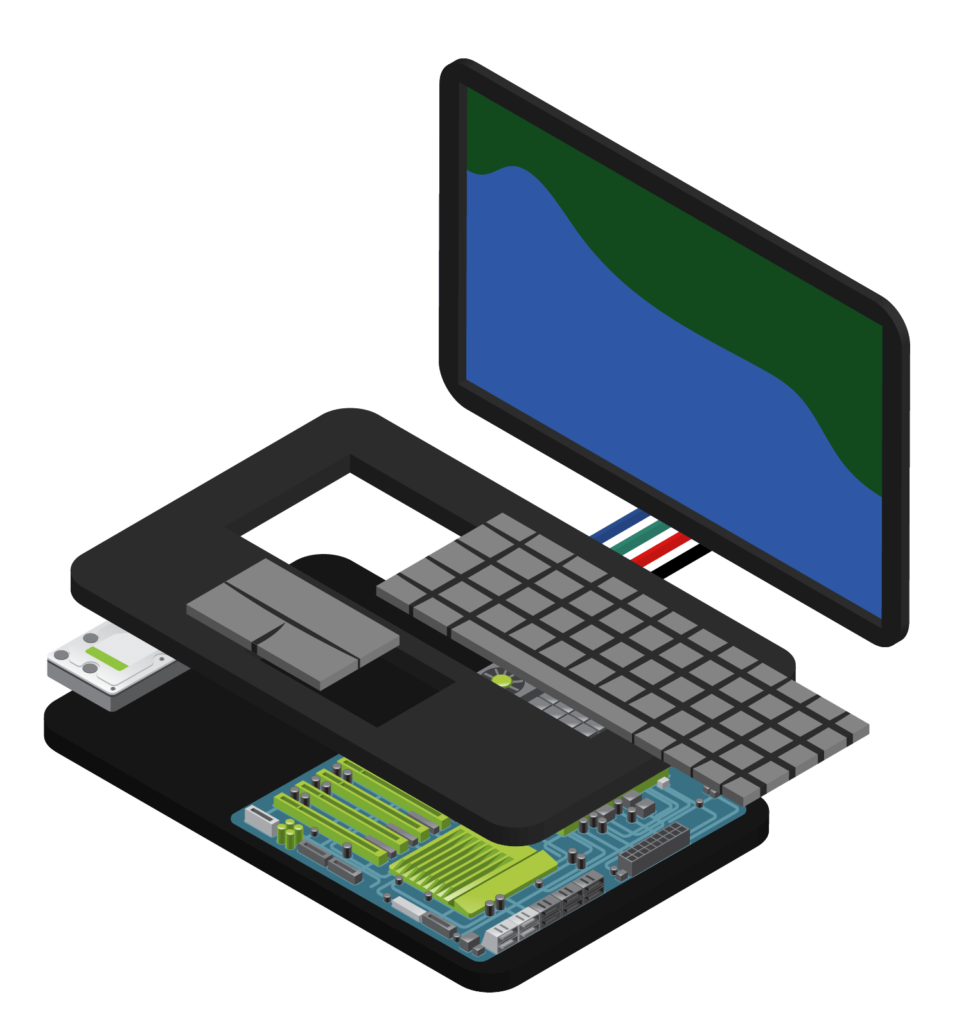
A word of warning about customizability.
Be aware that some options listed on a vendor’s data sheet may be available only in theory; they may never have been designed, built or tested. Even if they have been, they may not be fully built into the system; you may have to pay a significant additional charge to obtain them.
Ask about the options you need. Have they been tested and delivered to other customers? How will they affect delivery time? Is there an additional charge to obtain them?
It’s better to ask these questions ahead of time. As one systems integrator told us from hard experience, “When a manufacturer says you can have a given set of outputs, you don’t want to find out during integration that the units can’t supply them.”
Key consideration #3: Modularity
Modular design is a way of future-proofing the mission computer. It is designed so its physical form factors, both internal and external, never change. This allows the units to be easily upgraded as needs and technologies evolve.
As years pass, if you need greater performance, you can choose to either upgrade your existing units or replace them with a newer version. In either case, you’ll be buying slot-in replacements for your existing equipment, whether those be components, boards or entire LRUs. Connectors and cabling will be unaffected.
Modularity improves long-term supportability. It keeps units in service longer and pushes installation changes far down the road. It means you’ll never hear your supplier say things like, “Oh, our new units have a different form factor and connector arrangement, so you’re going to have to change your rack, cables and connectors,” or, “Sorry, this computer was built around a bespoke board, and the board manufacturer went out of business; you can’t buy additional units any more.”
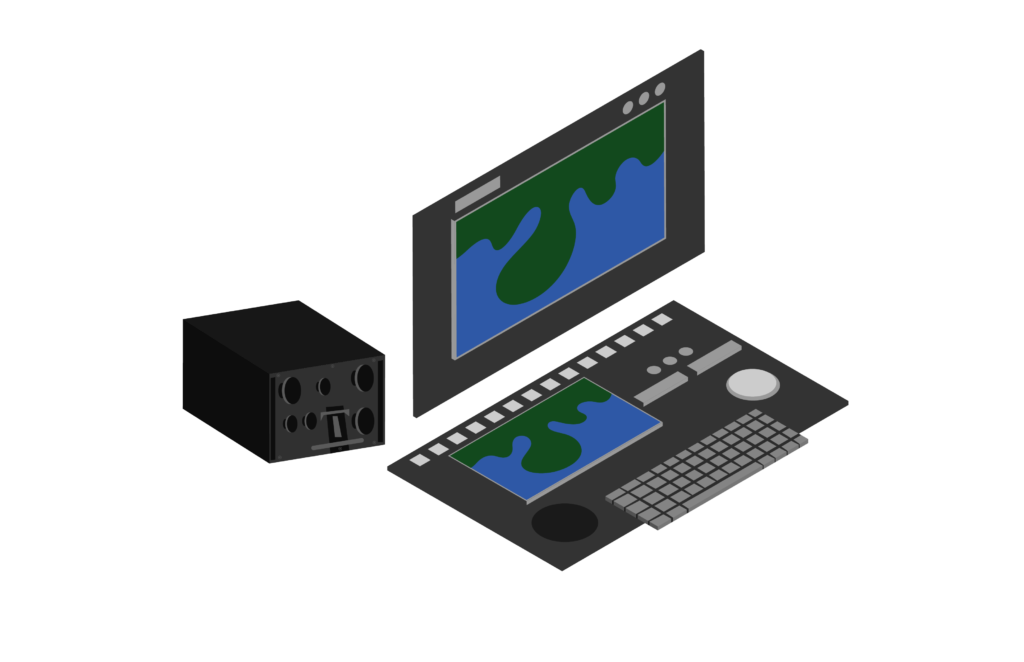
Key consideration #4: Custom backplane option
Many mission computers have a fixed set of connectors that can’t be changed to suit individual customers.
But what if you have, say, ten computers from Supplier A in service and Supplier A goes out of business? What happens when you need to upgrade those ten computers, because you need better performance for the new software you want to run? You really don’t want to dismantle ten airframes, rip out all their cabling and replace all their connectors.
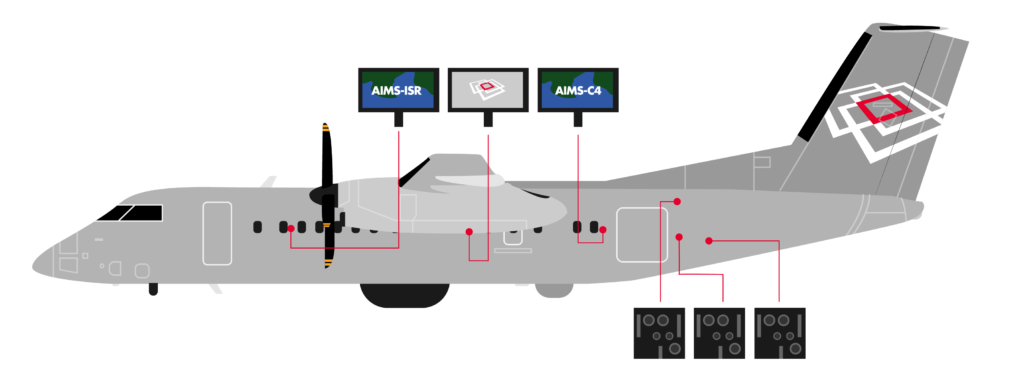
An inexpensive solution for this problem is a custom backplane.
Some suppliers have designed their computers to accommodate a custom backplane with minimal change to the rest of the system. These suppliers can design you a bespoke backplane that matches your existing connectors pin for pin, and they can supply them to you in small quantities with a limited NRE burden.
Download the Guide + Checklist
The printable guide + checklist is now available!
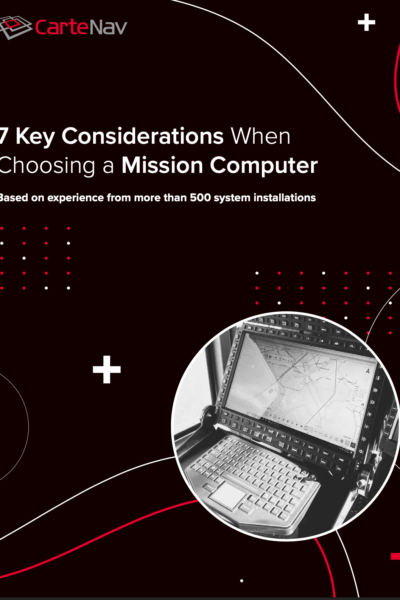
Key consideration #5: Two computers in one box
Operators in roles such as law enforcement, maritime patrol, and fire mapping frequently need two crew members operating different sensors simultaneously. System integration contracts for such missions often include a clear-cut requirement for two mission computers.
Of course, you’ll need to find space for every LRU you install. You’ll also have to run cables from other systems and find space for all that cabling. And the more equipment and cabling you install, the more weight you add to the platform.
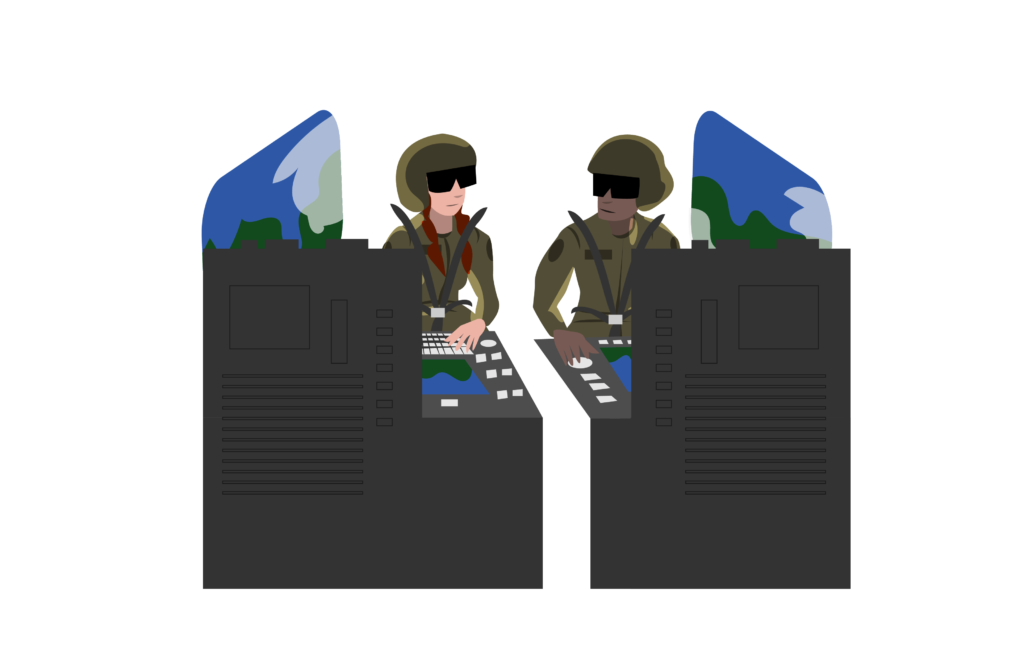
But what if you could have two completely independent mission computers in one box? At least one supplier we know offers such a system.
Putting two mission computers in one box greatly lowers customer costs. That’s because the cost of the computer hardware is trivial compared to the cost of installation, integration, and certification of two LRUs.
Mission computer weight and volume are reduced by nearly half. You install half the cabling. Your airworthiness certification paperwork is slashed by half as well. Overall, this two-in-one approach greatly reduces the burden on the system integrator. In short, it cuts your headaches in half.
Key consideration #6: Inside-the-box options
Look for other onboard integration of components that might otherwise be external, such as video encoders and ethernet network switches.
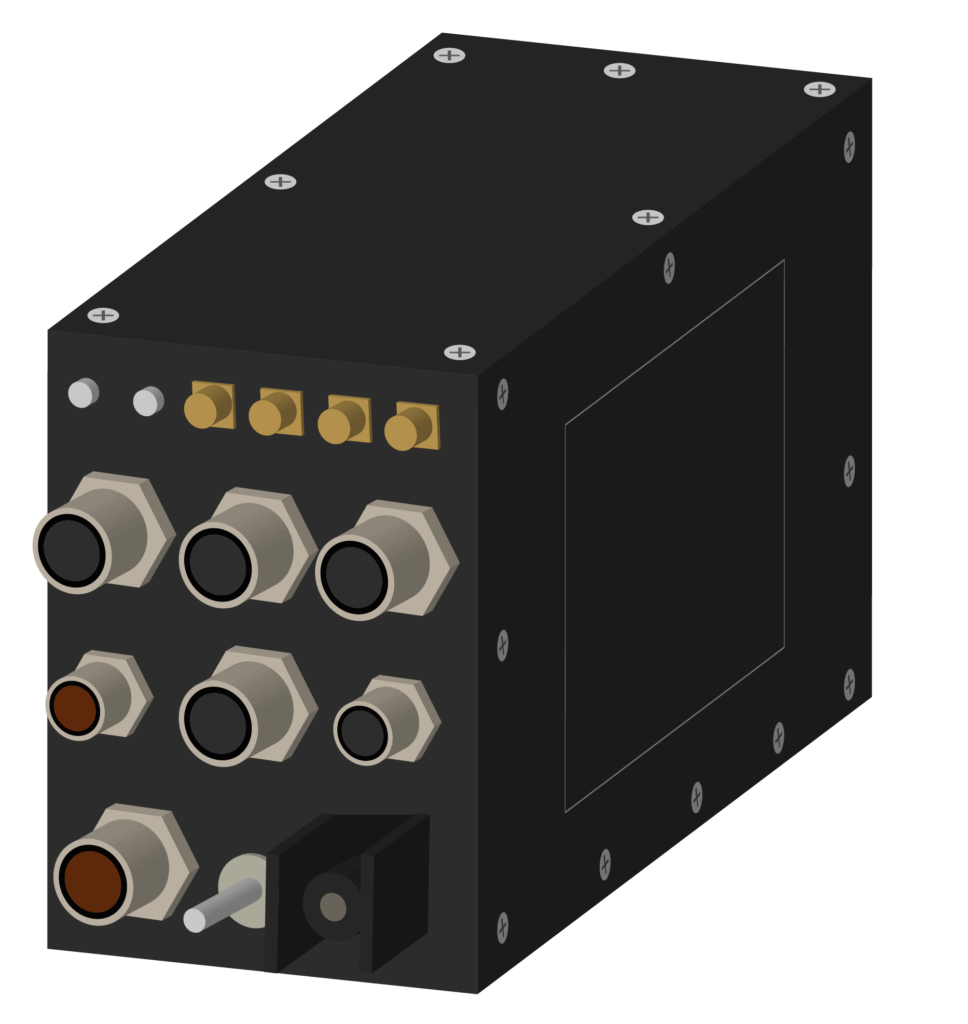
Like the dual mission computers just discussed, these options save space and weight, simplify cabling and installation, and help streamline certification.
The VPT-Mantis-I computer, for example—a computer designed specifically to run CarteNav Solutions’ AIMS-ISR mission software—offers several integrated video encoder options along with a five-port gigabit ethernet network switch on board. This allows inputs from your gimballed turret and other sensors to be routed directly to the mission computer while eliminated the need of two additional LRUs.
Key consideration #7: Maximize headroom
Maximizing headroom means making allowances for growth down the road. (It has nothing to do with Max Headroom, the pseudo-AI TV personality of the 1980s.)
If you’ve owned a PC for a while, you know that the software you’re running today is much different than what you were running when you first bought the machine. Much of it has likely been upgraded multiple times. As your needs have changed, you’ve added new applications. And over time, you’ve seen a gradual drop in performance.
Of course, how fast that performance drops—and how long you’re able to use your PC before replacing it—is a function of your PC’s specifications when you bought it.
Mission computers are no different.
So, don’t skimp on performance and future growth potential during initial installation. Don’t buy a processor that’s simply “adequate” for the missions you’re performing, the payloads you’re carrying, and the software you’re running today. The same goes for RAM, disc capacity, communication ports and other features.
You never know what could be coming tomorrow. A new mission or a change in mission requirements could call for new payloads or new applications.
Also, be aware that mission computers that have been on the market for a few years may be using processors and other hardware components that are several generations older than the current state of the art.
Other considerations
To close, here are a few other things to consider when you’re evaluating mission computers for your next installation or retrofit:
Physical size: Is it going to fit in the space provided?
Weight: Will it be too heavy for the equipment rack or the aircraft?
Removable data drives: Can these be easily inserted and removed? Thumb screws make it easy for the crew to accomplish this task. If a tool is needed to access the drive, it is probably a job for a technician, not a crew member.
Cooling: If the unit uses passive cooling (a heat sink) is there enough airflow around the unit? If it uses internal fans, can hot air escape from the equipment rack?
Portable: Will a portable electronic device (PED)—such as a tablet computer with keyboard—meet the requirements? Use of PEDs eliminates STC requirements and modification design approvals.
Monitors for portable devices: Should be touchscreen compatible. Look for a minimum resolution of 1920×1080.
Additional Ports: Look for external remote reset switches and remote USB ports (USB 3.0 recommended).
Docking stations: Can the PED be docked and linked to external monitors/keyboard/mouse?
Power supplies/dc converters: Are they rated correctly?
Graphics card: Must support Open GL.
Network ports: Minimum of two.
Conclusion
At the end of the day, a mission computer is just that: a computer. But mission computers are not all created equal.
If you are currently shopping for a new mission computer or expect you will be soon, be sure to have this guide and the accompanying checklist handy when you are evaluating candidates.
Download the Guide + Checklist
The printable guide + checklist is now available!
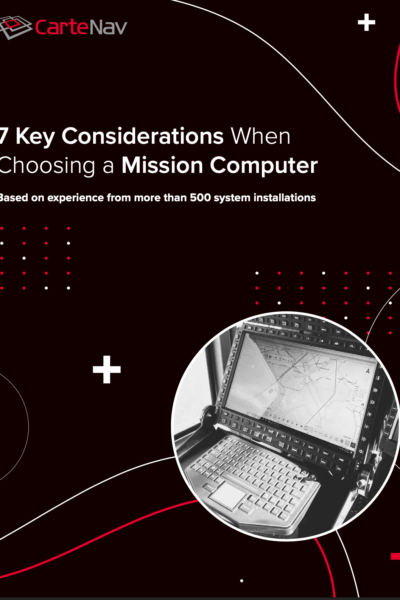
A thank-you to our partners
CarteNav Solutions would like to thank all our partners and suppliers who contributed their expertise to make this guide possible, with special thanks to Viewpoint Systems, manufacturers of the VPT-Mantis-I computer designed for AIMS-ISR.